How to Avoid Choosing the Wrong Materials for Your Custom Decals
Transparent polyurethane, raised domed, heat resistant, magnetic backed, UV stabilised…
I just want milk that tastes like real milk.
Some of our clients are passionate about understanding the chemical and technical nature of the materials used in their custom labels. However, most just want confidence that their labels will withstand the rigours of the environments that their products are exposed to.
That's what we're going to unpack in this article.
The materials required for compliance plates on excavation machinery in a Pilbara mine differ from those we will use for product labelling commercial baking equipment, which will be different again from those used for a real estate agency's name tags.
To avoid creating an article full of "it depends" types of insights, we have outlined below custom decal and custom label material options that are generally a good fit solution for the nominated applications.
However, before resolving to choose a labelling solution from a list, we strongly believe that every great label starts with a consultation to ensure it enhances your brand equity without blowing the budget.
Common Custom Label Requirements
Clients, generally speaking, have two determining factors when chasing a labelling solution:
-
“I want it to last a long time without diminishing, e.g. fading or peeling.”
-
“I want it to be cost-effective.”
Let’s explore common materials when desiring a long-lasting, cost-effective custom-label solution.
Domed Labels
What Are Domed Labels?
Domed labels, also known as raised or 3D stickers, feature a clear, dome-shaped polyurethane coating over a printed design. They come in a variety of sizes, from just a few millimetres to several metres, and their glossy, eye-catching appearance makes them a popular choice for businesses looking to create labels that truly stand out.
However, not all domed labels are created equal. There’s often confusion around the different types, but the key distinction lies in the resin used to create the signature raised, glossy effect.
Epoxy vs Polyurethane Resin: What’s the Difference?
Two types of resin are commonly used in domed labels: epoxy resin and polyurethane resin. While they may appear similar at first glance, their properties and performance differ significantly. Below is a summary of the differences, but you can see the more detailed explanation here.
- Polyurethane Resin:
This flexible resin is designed to resist discolouration, fading, cracking, and scratching. It’s highly durable and offers exceptional UV, chemical, and water resistance, making it an excellent choice for outdoor applications. - Epoxy Resin:
A thicker, harder material that offers strong impact resistance. However, it’s more prone to cracking, fading, and discolouration over time, particularly in harsh environments.
When durability and longevity are key—especially in challenging conditions—polyurethane resin is the superior choice.
Why Choose Domed Labels?
Domed labels are ideal for products exposed to outdoor weather, harsh sunlight, or chemicals. Their durability ensures they won’t peel, fade, or fall off, making them a reliable solution for demanding environments. While they may come at a higher price point, their performance and longevity make them a worthwhile investment.
Polycarbonate Labels
Polycarbonate, often called "polycarb," is a strong, lightweight, and virtually indestructible plastic, making it an excellent choice for creating long-lasting labels.
Much like domed labels, polycarbonate labels are highly resistant to UV rays, chemicals, water, and extreme weather conditions. However, while domed labels boast a raised, glossy profile for visual impact, polycarbonate labels feature a flat, sleek design. This understated look makes them ideal for applications where durability is critical, but a simpler, more functional appearance is preferred—such as labels displaying vital information.
Common Uses for Polycarbonate Labels
Polycarbonate labels are versatile and often used in:
- Graphic overlays
- Control panels
- Nameplates
- Panel fronts
- Labels for high-touch products
Industries That Rely on Polycarbonate Labels
Polycarb labels are a go-to solution for various industries, including:
- Automotive: For dashboards, consoles, and component labelling.
- Electronics: Used in devices requiring durable overlays or controls.
- Manufacturing: Ideal for heavy-duty equipment labels and nameplates.
Why Choose Polycarbonate Labels?
Polycarbonate labels are engineered to endure physical stress and harsh conditions, reducing the need for frequent replacements. Their exceptional durability ensures that your products remain clearly identified and protected, even in the toughest environments. By choosing polycarb labels, you’re investing in a reliable labelling solution that stands the test of time.
Choosing the Right Materials for Your Custom Decals
Selecting the right label material involves more than just aesthetics. Ask yourself:
- What environment will the labels be exposed to?
- What surface will they adhere to?
- What information will they display?
Taking these factors into account is essential for ensuring your labels and decals perform reliably and stand the test of time. To make the best decision, consult with industry experts who can provide tailored advice based on your specific needs. By analysing these factors beforehand, you’ll give them the insights they need to recommend the most suitable material for your application.
The Cost of Choosing the Wrong Material
The consequences of selecting the wrong label material can be significant, affecting both your operations and your bottom line. Common issues include:
- Product damage
- Harm to your brand's reputation
- Costly rework and project delays
As the old saying goes, "you get what you pay for." While budget-friendly labelling solutions may seem appealing, they often come with hidden costs. Inferior materials can lead to premature failure, meaning you'll spend more on replacements and damage control in the long run.
Investing in high-quality materials and seeking expert guidance upfront can help you avoid these pitfalls. It’s a smarter choice that ensures product integrity, reliability, and ultimately, better value for your money. After all, no one likes to pay twice for the same mistake.
Your Custom Decal Materials – Final Thoughts
Domed and polycarbonate labels are exceptionally durable, designed to perform reliably even in the toughest environments. Whether you’re after a sleek, modern appearance or a robust, protective finish, these materials deliver outstanding performance and longevity. By evaluating your specific requirements, you can choose the perfect label solution to ensure your products are clearly identified, visually appealing, and built to last.
You May Also Like
These Related Stories
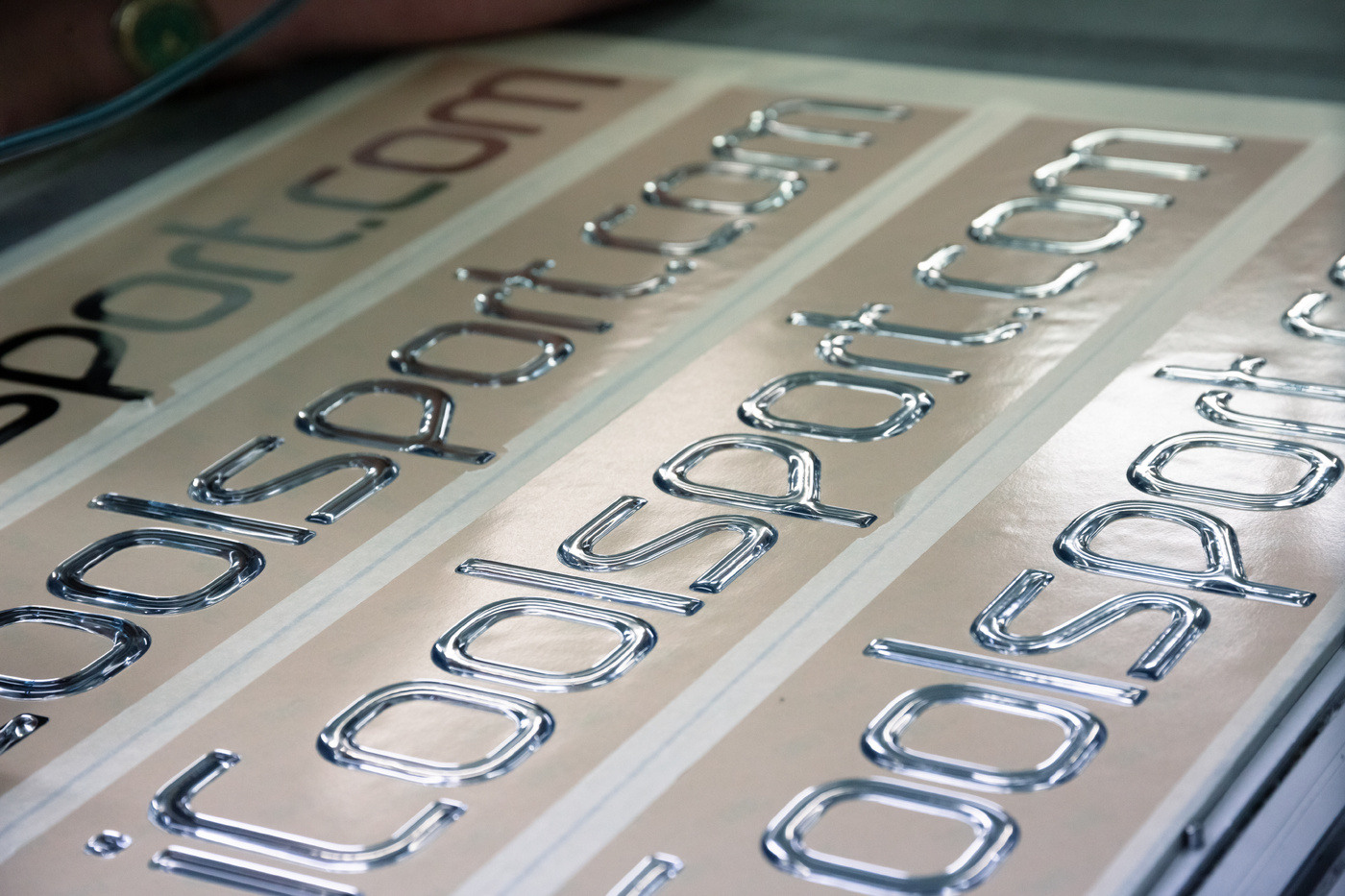
How Custom Labels Can Increase Brand Equity Without a Budget Blowout
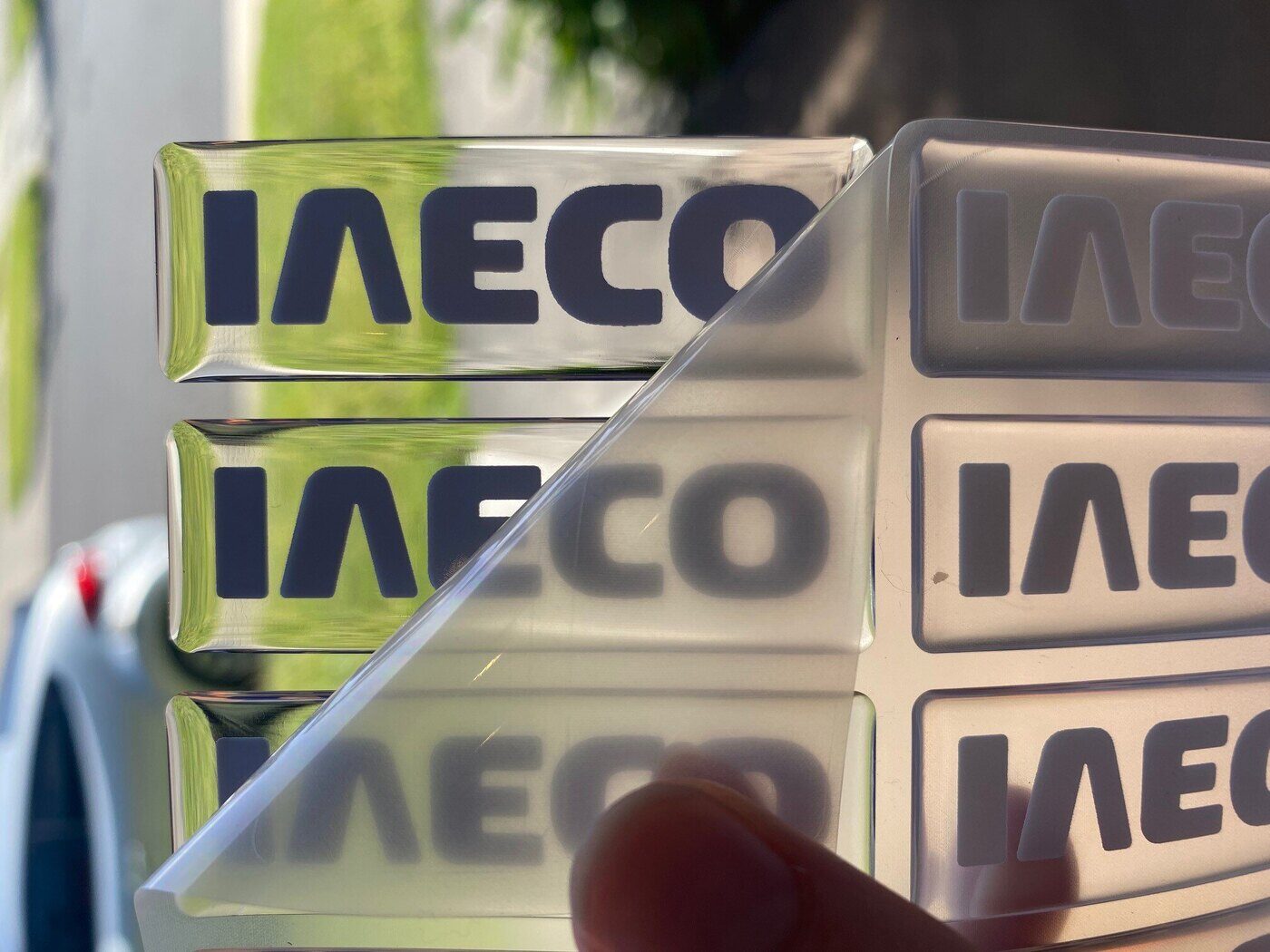
How to Stop Your Custom Labels from Peeling and Falling Off
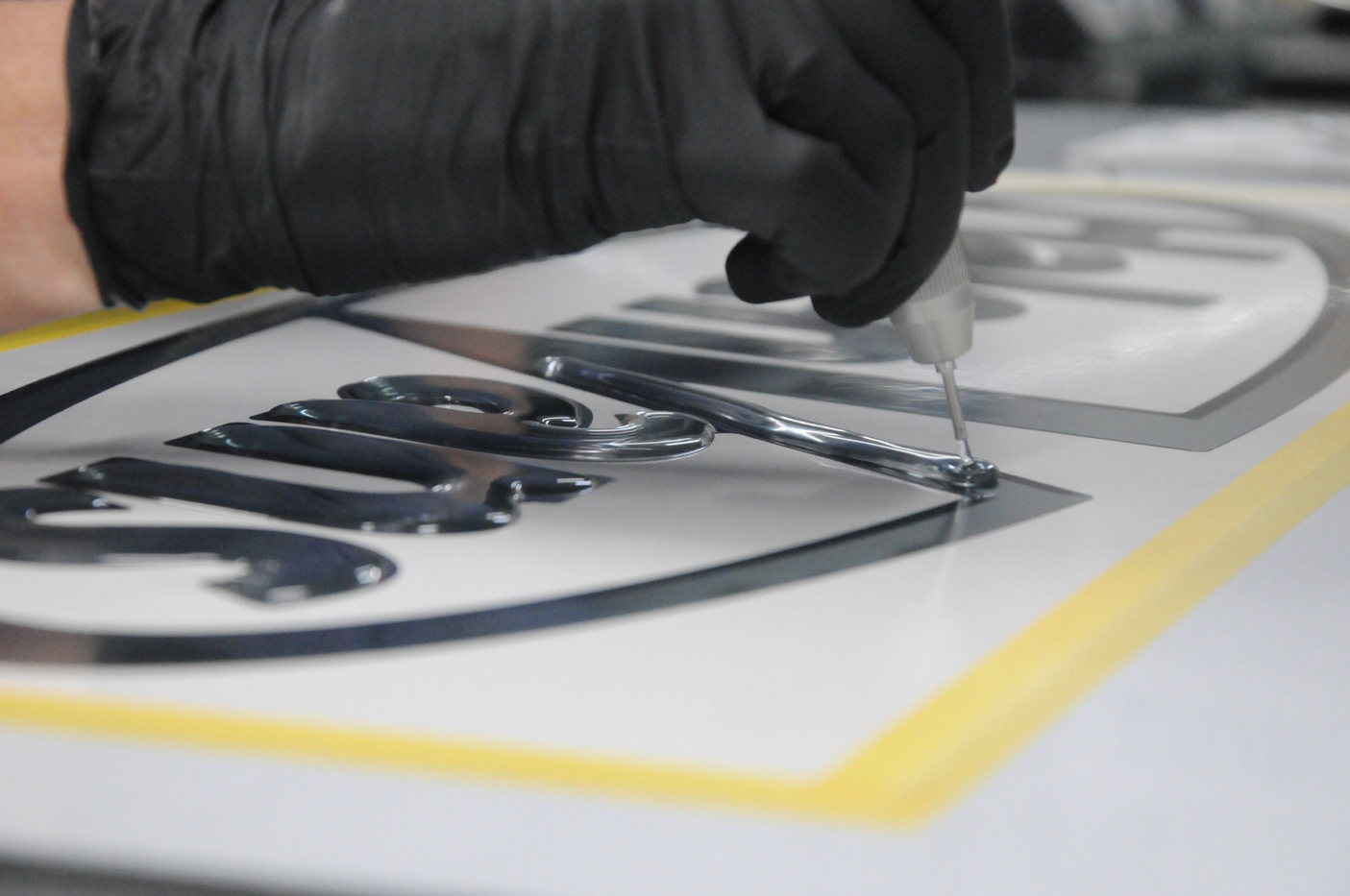